Our Services
3D printing for IZS (Integrated rescue system)
Our long-term cooperation with the IZS also brings interesting prototype and subsequent “small series” production of unique parts. We use several types of 3D printing, or additive manufacturing.
FDM printing
FDM (Fused Deposition Modeling) printing is a 3D printing technology that uses thermoplastic materials such as PLA, PETG, TPU, ABS, ONYX (PA-CF) or PAHT-CF. The print head melts the material and applies it layer by layer to the print surface, where the material cools and solidifies.
For FDM printing we use Makforged Mark X3, Markforged Mark Two and Bambulab X1 Carbon printers. We print final objects mainly from Onyx, PLA or PETG materials. Alternatively, we can add carbon fiber or Kevlar (similar to fiberglass) to the individual layers of Onyx to reinforce the final product.
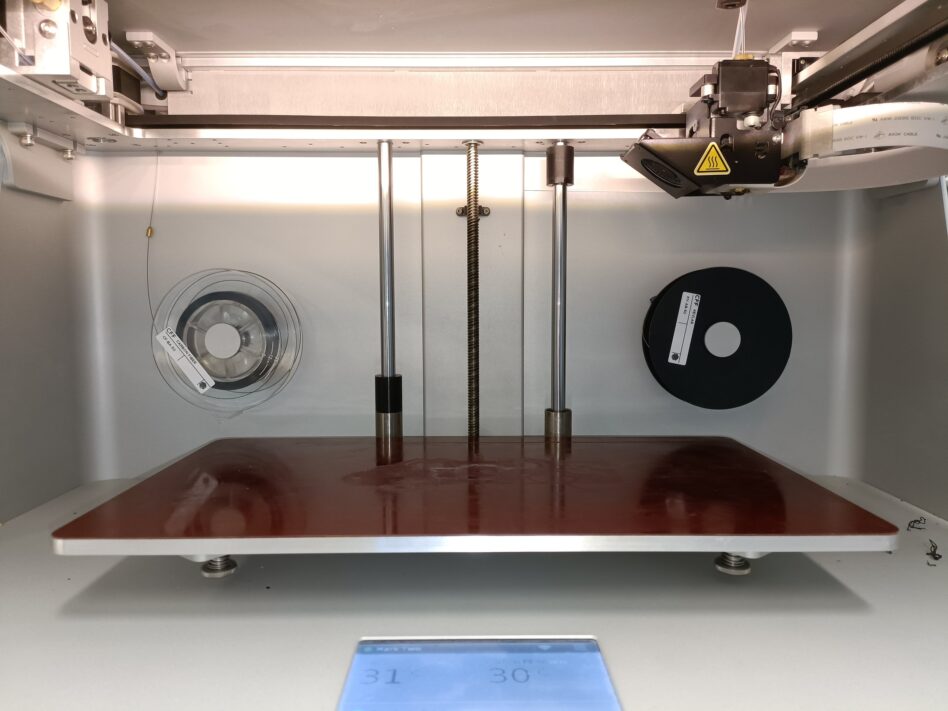
Onyx (PA-CF)
Onyx (PA-CF) is a nylon with chopped carbon microfibre filler. It is the ideal material for stiff, strong and accurate prints, which can also be reinforced with any of the available continuous fibres. Onyx is also a step ahead in surface accuracy, chemical resistance or heat resistance compared to conventional plastic materials. This makes it an ideal material for the manufacture of various components for firefighter equipment. For the Fire Department we print various adapters for flashlights and helmet cameras, or docking stations for cameras and more.
PLA and PETG
PLA and PETG materials are less rigid than Onyx and are therefore used mainly for components that are not expected to be subjected to extreme loads or for testing purposes. The advantage of these materials is also their chemical neutrality. This is why we use them for example for printing lung automation controllers for the Fire and Rescue Service, or for printing bone prototypes for training medical personnel.
SLS printing
SLS (Selective Laser Sintering) printing is a 3D printing technology that uses powder materials such as PA12 (Nylon12). The print area is gradually covered with a layer of powder, which is then laser sintered at specific points to create the model. This process is repeated until the entire object is finished. When the printing is complete, the model is removed from the printing chamber and the remaining powder is recycled. SLS printing allows complex geometric shapes to be created without the need for supports.
Within the SLS technology we use the Formlabs Fuse1+ printer and print specifically from PA12 material. We use this technology primarily for printing larger numbers of pieces or for printing larger geometrically complex parts.
Comparison of materials used for the Fire and Rescue Service
Výhody | Nevýhody | |
---|---|---|
PA-CF (Onyx) | ▪ Strong, flexible and durable material.
▪ Possibility of reinforcement with different types of fibres. ▪ Faster development for simpler parts. |
▪ More expensive material.
▪ Printing can be limited by creating complex geometric shapes. ▪ Due to the printing technology, the printing itself is slower. |
PA12 (Nylon12) | ▪ Sand texture, which gives more adhesion to the material.
▪ Harder than Onyx. ▪ Any geometric shape can be printed. ▪ Full-wall components. ▪ Fast printing, possibility to fill the entire volume of the print chamber. ▪ Printing without the need for supports. |
▪ More demanding printing.
▪ More fragile than Onyx. ▪ More complex part prototyping. ▪ Reduced mechanical properties. |
Testing 3D printed sleeve adapters
In order to verify the durability of the printed parts, we took part in testing them together with the Fire Brigade. The sleeve adapters were tested by firefighters in the training centre of the Fire Brigade Zbiroh. During the day, several training situations took place, in which the training firefighters were equiped with helmets with socket adapters created by 3D printing from the materials mentioned below.
Materials tested:
• Onyx (FDM printing)
• PA12 (SLS printing)
• PAHT-CF (FDM printing)
In the first photo, firefighters are testing a situation in which a flame is ignited (by the ignition of a liquid gas) that spreads rapidly across the ceiling of a room. The firefighter’s helmet, equipped with printed sleeve adapters, is briefly exposed to temperatures of around 400°C.
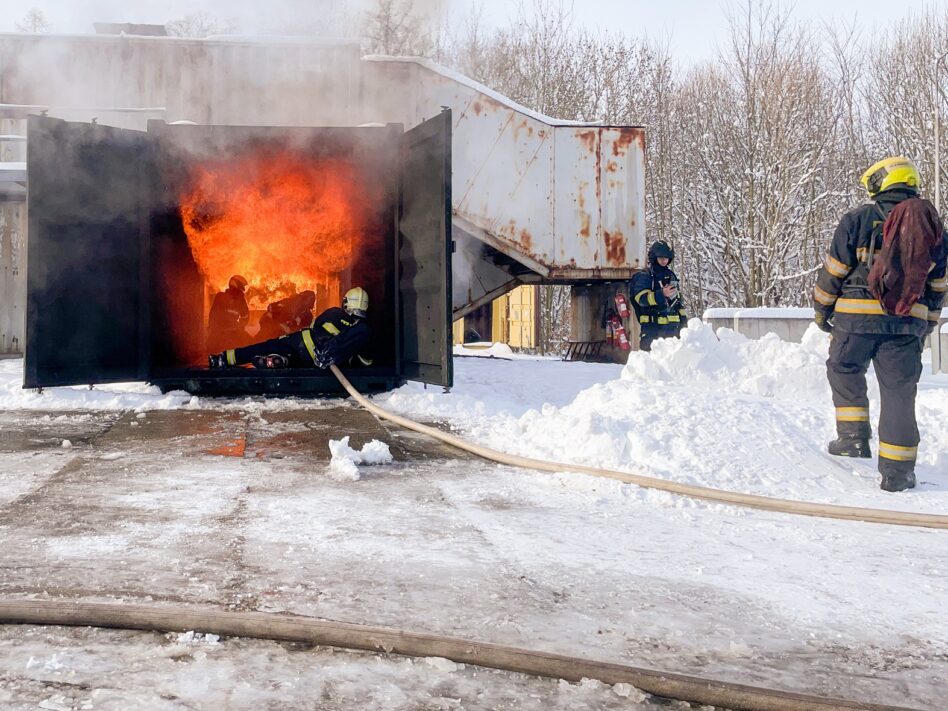
The other two photos show firefighters training in the so-called observation container, where heat radiates up to 700°C from the ceiling sheets. At the same time there is a hot heat flow (about 120°C) around the helmets of the firefighters. In this container, firefighters practice staying in a hot, densely smoke-filled area, watching the development of the fire and assessing the different stages of smoke.
All the tested materials have passed the above conditions and meet the requirements of the Fire Brigade representatives.
Please find attached a catalogue of our standard 3D models. If you also own a 3D printer or have the opportunity to 3D print, you can download the models created by us free of charge from our website, see links below this post.
Downloads
-
3D Prints Catalogue
Format: pdf, size: 577 KB -
Transmitter holder
Format: stl, size: 8 MB -
ID01 SLS Camera holder SenaCubeWifi
Format: stl, size: 2 MB -
ID02 SLS Camera holder MiVueM700
Format: stl, size: 1 MB -
ID03 Adapter DrägerHPS7000
Format: stl, size: 1 MB -
ID04 Adapter DrägerHPS3500
Format: stl, size: 892 KB -
ID05 Flashlight holder
Format: stl, size: 1 MB -
ID06 Swivel pin AirBusTPH900
Format: stl, size: 671 KB -
ID07 Clip with swivel pin AirBusTPH900
Format: stl, size: 1 MB -
ID08 Frame AirBusTPH900
Format: stl, size: 994 KB -
ID14 Adapter for Rosenbauer heavy duty helmet
Format: stl, size: 1 MB
Every new contract for us always has the same and only goal - success and a maximally satisfied client.
Contact us